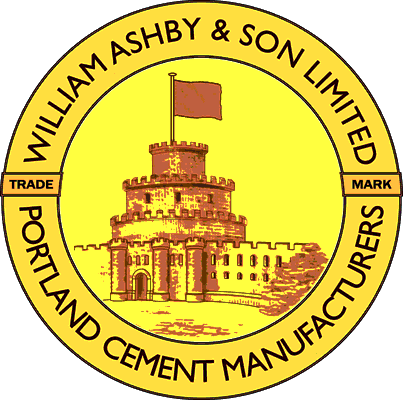
William Ashby & Sons Portland cement logo
Location:
- Grid reference: TQ39167905
- x=539170
- y=179110
- 51°29'38"N; 0°0'17"E
- Civil Parish:Greenwich, London
Clinker manufacture operational: 1852-1926
Approximate total clinker production: 410,000 tonnes
Raw materials:
- Upper Chalk (Seaford Chalk Formation: 85-88 Ma) was obtained from commercial suppliers. They were buying from NCBC in the 1890s. A barge-load a day would have kept them going.
- Possibly Medway Alluvial Clay. They referred to it as "mud".
Ownership:
- 1852-1867 Henry Reid
- 1867-1926 William Ashby and Son Ltd
The plant was set up on a cramped site on Primrose Wharf by Henry Reid in 1852. The site, north of that of Edwin Hollick, was still given as owned by Henry Reid in a 1867 directory. The site may previously have been used to make “Roman Cement”. Reid took on management of the Elmley plant in 1865. From 1852 to 1856, Reid was in partnership with John Winkfield, owner of the Hollicks site.
William Ashby and Son started in the pre-Portland era, also making Roman cement, at Isleworth. The son, George Crowley Ashby (b Staines 1812, d Isleworth 1893), obtained the sub-lease of the site on 21/10/1867, although he remained for the rest of his life resident in Isleworth. He retired in 1887, his son John Dickie Ashby (b Isleworth 1863, d Catford 1920) taking over management of the Greenwich plant. At the same time, the Isleworth plant was shut and Roman cement production ceased. A period of decline followed, and in 1892 the company was liquidated and re-formed with added capital from George Crowley Ashby's nephew, consultant engineer Charles Ashby Lean.(b Ebbw Vale 1844, d Rio de Janeiro 1902). Francis says that the Greenwich plant produced 7,500 t/y in the early 1880s, and was uprated in 1892. Davis puts the 1907 capacity at 400 T/week.
The original site occupied only 0.73 Ha with 33 metres of waterfront: Primrose Wharf. Maps show multiple stages of development. The initial Portland cement plant was wet process, with 1422 m2 taken up with slurry backs. There were about 700 m2 of drying flats heated by coke ovens, and five small bottle kilns of total capacity 60 t/week (presumably originally for Roman cement). In 1882 the site was extended by 0.27 Ha and a bank of three larger kilns (90 t/week) was added. Up-rate of the plant using bottle kilns was impossible because of lack of space for slurry backs, but conversion to the much more compact chamber kiln operation began in 1891 – with the conversion of three bottle kilns to Batchelor kilns (80 t/week). This bank was expanded by two (40 t/week) in 1893, then perhaps around 1900 a set of three (90 t/week) was built over part of the drying flats, indicating abandonment of the bottle kilns. In the period up to 1907, blocks of three (90 t/week) and four (110 t/week) were added.
Absorption into BPCM was discussed but turned down. With a total chamber kiln capacity of 410 t/week, a prime location, and a captive market through the firm’s builders’ merchants, the plant was able to struggle on against price-cutting by the more efficient competitors, but finally shut in 1926, perhaps with the General Strike – the plant had no storage space at all, and cessation of supplies of coke and chalk would have stopped it instantly. There was no rail link, all product being despatched by barge. The site continued in use by Ashby’s for movement of building materials until WWII, then was absorbed into the Molassine Meal plant to the north, later acquired by Tate and Lyle, and currently the Amylum sugar refinery.
Power supply
The plant was direct-driven by two 180 HP steam engines.
Rawmills
There was a series of washmills, number uncertain.
No rotary kilns were installed.
Sources::
- Primary Sources:
- Newspaper articles
- Mary Mills, Greenwich Peninsula, Greenwich Marsh: History of an Industrial Heartland, Amazon, 2022, ISBN 979-8669957155
- Ashby papers: Croydon Archives Ref. AR948
- Newspaper articles
- Aerial photography
- Ordnance Survey 1:2500 mapping
- Confirmatory Sources: