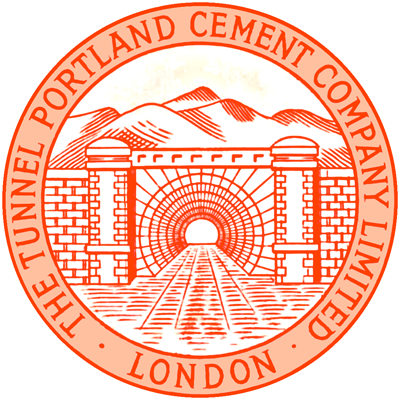
1940s Tunnel Brand
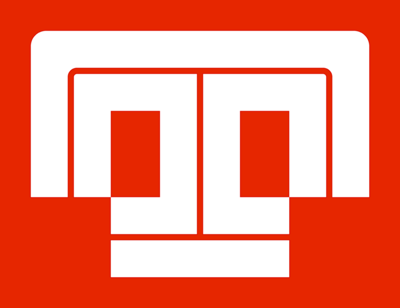
Big T Brand used from the late 1960s
Location:
- Grid reference: SP93431525
- x=493430
- x=215250
- 51°49'41"N; 0°38'39"W
- Civil Parish: Pitstone, Buckinghamshire
Clinker manufacture operational: 1937-1991
Approximate total clinker production: 22.7 million tonnes (18th)
Raw materials:
- 1937-1969 Grey Chalk (Zig-zag Chalk Formation: 94-97 Ma) and Chalk Marl (West Melbury Marly Chalk Formation: 97-100 Ma) from quarry at 493900,214600 extending south into Marsworth, Buckinghamshire: brought to plant washmill by rail.
- 1969-1991 Grey Chalk and Chalk Marl from quarry at 493300,214200 in Marsworth, Buckinghamshire: bucket wheel excavator supplying plant by conveyor.
- 1953-1991 Middle Chalk (Holywell Nodular Chalk Formation: 92-94 Ma) and Grey Chalk from quarry at 494500,214400 extending south into Aldbury, Hertfordshire: 1953-1969 washed on site and pumped to the plant: 1969-1981 bucket-wheel excavator supplying to plant by conveyor: 1981 BWE replaced with back-actor and crusher.
See also an in-depth article on The Chilterns.
Ownership:
- 1937-1968 Tunnel Portland Cement Company Ltd
- 1968-1986 Tunnel Cement Ltd
- 1986-1991 Castle Cement Ltd (RTZ to 1989, Scancem to 1991)
Pitstone was Tunnel’s first green-field site, and the last to be established in the Chilterns. The land, which was part of the recently broken-up Bridgwater and Pendley Manor estates, was first earmarked for cement production in 1927, by a speculative company using Edgar Allen as plant supplier, which failed to raise sufficient capital. The land contained a wide outcrop of soft chalk marl, with high-grade chalk at the foot of the Chiltern escarpment. The high-grade proved adequate for white cement manufacture from 1957 to 1972. The plant grew one kiln at a time, with relatively inefficient wet process kilns, ameliorated by the very low processing cost of the raw material. The plant made sulfate resisting clinker alongside ordinary clinker from 1954 to 1991.
Following the straightforward installation of the long dry kiln at Padeswood, kiln A5 was established as an autonomous production unit, and was the only modern British attempt to apply dry processing to wet chalk, using kiln exhaust gas for raw material drying. The raw material, ideal in all other respects, had average 15% moisture content, and required a high temperature throughout the drying circuit to prevent blockages, so it proved impossible to reduce the heat consumption below 5 MJ/kg – a performance achieved by many wet process kilns. The plant was finally killed off by the 1991 downturn. Part of the shell of A5 was used as Padeswood A4. Transportation was by rail: in fact the London-Birmingham main line effectively decided the location of the plant. The site is now an industrial estate, The earlier marl fields were returned to agriculture and have more recently been developed for housing; the later quarries are partially flooded waste.
Please contact me with any relevant information or corrections. I am particularly interested in firmer dates and statistics.
Power supply
The entire plant was electrically driven, using power purchased from the grid from the outset.
Rawmills
The wet process plant used washmills with Trix screeners and ball mill grinding screener rejects, the system being extended as kilns were added. A separate plant was constructed for white rawmix preparation. The dry process plant had used three crusher-driers fed with hot exhaust from the preheater. The fine product was classified, the oversize going through an air-swept regrind ball mill also fed with exhaust gas. The fine feed then passed into a conventional dry-blending system before being fed to the pre-heater riser.
Five rotary kilns were installed.
Kiln A1
Supplier: FLS
Operated: 20/09/1937-05/1979
Process: Wet
Location: hot end 493377,215217: cold end 493468,215227: hot end enclosed
Dimensions: Metric 91.85 × 2.700B /2.250C / 2.850D
Rotation (viewed from firing end): clockwise
Slope: 1/25 (2.292°)
Speed: ?
Drive: ?
Kiln profile: 0×2700: 27300×2700: 30000×2250: 60000×2250: 62700×2850: 91350×2850: 91350×2400: 91850×2400: Tyres at 6600, 19600, 35600, 51600, 67600, 85600: Turning gear at 37800.
Cooler: FLS bucket grate, with quenching on white production.
Fuel: 1937-1957, 1969-1971 Coal: 1957-1969 Oil: 1971-1979 Gas
Coal mill: indirect: ball mill
Exhaust: to ID fan followed by electrostatic precipitator to stack.
Typical Output: 1937-1945 267 t/d: 1946-1957 287 t/d: 1957-1972 220 t/d (intermittent white clinker production): 1972-1979 287 t/d
Typical Heat Consumption: 1937-1945 8.3 MJ/kg: 1946-1957 7.4 MJ/kg: 1957-1972 9.5 MJ/kg: 1972-1979 7.75 MJ/kg
Kiln A2
Supplier: FLS
Operated: 03/1952-05/1979
Process: Wet
Location: hot end 493377,215210: cold end 493475,215220: hot end enclosed
Dimensions: Metric 98.00 × 3.000BC / 3.450D
Rotation (viewed from firing end): clockwise
Slope: 1/25 (2.292°)
Speed: ?
Drive: ?
Kiln profile: 0×3000: 62450×3000: 66000×3450: 97500×3450: 97500×3000: 98000×3000: Tyres at 10150, 33650, 57150, 86950: Turning gear at 60000
Cooler: Folax ?624 grate.
Fuel: 1952-1957, 1969-1971 Coal: 1957-1969 Oil: 1971-1979 Gas
Coal mill: indirect: FLS Tirax ball mill
Exhaust: to ID fan followed by electrostatic precipitator to stack.
Typical Output: 1952-1962 368 t/d: 1963-1971 376 t/d: 1971-1979 383 t/d
Typical Heat Consumption: 1952-1962 6.85 MJ/kg: 1963-1971 7.45 MJ/kg: 1971-1979 7.2 MJ/kg
Kiln A3
Operated: 11/1954-05/1979: 06/1987-1990
Location: hot end 493382,215170: cold end 493479,215181: hot end enclosed
Fuel: 1954-1957, 1987-1990 Coal: 1957-1972 Oil: 1972-1990 Gas
Typical Output: 1954-1962 388 t/d: 1963-1971 385 t/d: 1971-1990 398 t/d
Typical Heat Consumption: 1954-1962 6.75 MJ/kg: 1963-1971 7.35 MJ/kg: 1971-1990 7.1 MJ/kg
Identical in all other respects to A2.
Kiln A4
Supplier: FLS
Operated: 11/1963-1990
Process: Wet
Location: hot end 493388,215183: cold end 493526,215198: hot end enclosed
Dimensions (from cooler ports): Metric 135.00 × 3.600BC / 3.950D
Rotation (viewed from firing end): ?
Slope: 1/25 (2.292°)
Speed: ?
Drive: ?
Kiln profile (from cooler ports):
Cooler: Unax planetary 10 × 11.50 × 1.400
Fuel: 1963-1971 Oil: 1971-1979 Gas: 1979-1990 coal, with 15% petcoke from 1986.
Coal mill: indirect: FLS Tirax ball mill
Exhaust: to ID fan followed by electrostatic precipitator to stack.
Typical Output: 1963-1971 671 t/d: 1971-1980 679 t/d: 1980-1990 671 t/d
Typical Heat Consumption: 1963-1971 6.75 MJ/kg: 1971-1980 6.55 MJ/kg: 1980-1990 7.55 MJ/kg
Kiln A5
Supplier: FLS
Operated: 01/1970-1991
Process: Long dry with 1-stage preheater, modified to 2-stage in 1980
Location: hot end 493583,214901: cold end 493446,214886: only cooler enclosed
Dimensions (from cooler ports): Metric 137.50 × 4.750BC / 5.250D
Rotation (viewed from firing end): anti-clockwise
Slope: ?
Speed: ?
Drive: ?
Kiln profile (from cooler ports): -18500×4750: 96250×4750: 100000×5250: 135750×5250: 137500×3450: tyres at -17500, 3500, 38000, 81500, 125000: turning gear at 75750.
Cooler: Unax planetary 10×14.40×1.800
Fuel: 1970-1971 oil: 1971-1980 gas: 1980-1991 coal, with 15% petcoke from 1986.
Coal mill: indirect: Claudius Peters ring-ball?
Exhaust: each of the three parallel crusher/driers was followed by a cyclone and ID fan followed by an electrostatic precipitator discharging into the stack.
Typical Output: 1970-1979 1057 t/d: 1980-1991 1272 t/d
Typical Heat Consumption: 1970-1979 5.35 MJ/kg: 1980-1991 5.15 MJ/kg
Sources:
- Primary Sources:
- Tunnel Cement (brochure), Tunnel Portland Cement Co., Ltd., 1950
- Pitstone 50 Years, Castle Cement, 1987
- “Extension of Pitstone Works”, Cement and Lime Manufacture, 41, January 1968, pp 13-16
- Ordnance Survey 1:2500 mapping
- BGS mapping and monographs
- Confirmatory Sources:
- Jackson, pp 249-250, 292-293