A series of articles appeared in the Engineering Record in 1897, describing to a primarily American audience the state of cement manufacturing technology in Europe. Although US production of Portland cement was still only one fifth of British production, its annual growth rate was over 50%, and 1897 was the first year in which indigenous production exceeded imports. Over 60% of production was by the rotary kiln, which had yet to be introduced in Europe. In the first of the articles (Frederick H. Lewis (Note 1), The European Cement Industry, The Engineering Record, XXXV, 1897) the British industry is epitomised, in descriptions of Hilton, Anderson and Brooks' plant at Grays, Essex, and Francis & Co's plants at Cliffe, Kent. The article appears to be out of copyright. It paints a picture of a British industry that is backward, and not in any immediate danger of becoming more progressive.
THE EUROPEAN CEMENT INDUSTRY
The most interesting fact at this time in regard to Portland cement in England is that the manufacturers have awakened to the necessity of improving their products. For twenty years methods of manufacture in England have remained practically unchanged, and the product changed as little as the methods. Portland cement was discovered by an Englishman; it got its name in England and for a quarter of a century its manufacture was wholly an English industry. The traditional policy of the manufacturers toward foreign trade has therefore been simply this: "Here is our cement as it has always been made; you can take it or leave it, for we make nothing else."
With the rise of the German cement industry, many foreign buyers have accepted the alternative, and German cements have displaced the English product in many export markets and quite generally command a premium in price (Note 2). This appears to have gone on without action in England until about two years ago, when the cement industry reached a crisis of small sales, little or no profit and financial stringency. Since then there have been large consolidations of interests, a better understanding in the trade, and a live interest among progressive men in studying the demands of export markets.
To American minds it must appear most extraordinary that manufacturers in England should have seen trade slipping away for years, and from sheer conservatism have been unwilling to take any steps to stop a loss both of business and of prestige. The real fact is that there have been several factors at work to bring about this state of affairs. The Englishman is conservative, but no one who knows the shrewdness of English business men can believe that they have let business decline from mere obstinacy. Two other factors which have contributed to the result described above are: 1. the conduct of manufacturing under land leases. 2. the obstinacy, not to say pig-headedness, of the English laboring classes.
The fabric of English law has been accumulating for centuries, much of it yet uncodified, and it is a veritable maze, which Dickens declared to be inexplicable until viewed from one standpoint. When you consider it as a device for making business for lawyers, the whole thing at once becomes perfectly clear. It is a real bar to change to an extent which is hardly realized in America, and in manufacturing as well as in agriculture, it evidently makes the improvement of leased property a matter for serious consideration.
The stubbornness of English labor in adhering to time-honored methods, and the power of the labor unions and of the close trades has often been commented on before. While the labor in England is energetic—" smart "—it evidently has more power and is harder to deal with than in either America or the continent of Europe. In a comparatively close industry like cement making, with the traditions of sixty years behind it, it evidently requires unusual vigor and determination to enforce new methods of work (Note 3).
At this writing this change of policy, inaugurated two years ago, has resulted in two changes of manufacture. The first is in putting finely ground cement on the market. It used to be considered quite good enough in England to grind cement so there should be a residue not exceeding 10 per cent. on a No. 50 sieve (Am. Soc. C. E. standard). Such cement gave good results in tests of neat briquettes, but when tested as in Germany and America in mixtures of 1 cement to 3 sand, the results were at least 30 per cent. to 40 per cent. below the figures obtained from finely ground cements. The sand-carrying capacity was essential, but was not there (Note 4).
To show what English manufacturers are now prepared to do, the following figures of a recent lot of cement shipped to America are here given:
- 99.9 per cent. passes No. 50 sieve.
- 95.0 per cent. passes No. 100 sieve.
- 78.0 per cent. passes No. 200 sieve.
These figures are in excess of any standard for fine grinding which has come to the writer's attention, and mark a really important improvement in quality (Note 5).
The second improvement is in making cement with a setting time to suit the conditions under which it is to be used. The old idea that a cement which was good enough for England was good enough for anybody is found to be an assumption which is neither true nor reasonable. It proves to be a fact that a cement which in the moist, cool climate of England will set in, say, 45 minutes, and which can be satisfactorily used there for any purpose, will in the warm, dry atmosphere of an American summer set in from two to five minutes and be quite unfit for laying sidewalks, or for any but rapid work. From a careful comparison of data in England and on the Continent the writer finds that: cements leaving Europe with a setting time of from five to eight hours will in America set in less than half these periods. Such changes appear to be quite marked even in winter, when the climatic differences are not great; but they are, of course, much more marked in summer. Even with very great care very queer changes in setting time take place in Portland cements, and the most experienced manufacturers are occasionally nonplussed to account for them. These facts have been receiving great attention from at least two leading English manufacturers in the last two years, and they now declare themselves ready to furnish whatever their customers may desire in this respect (Note 6).
Taken in conjunction with the fine raw material of the Thames and Medway, these two improvements evidently go a long way in improving English cement.
THE WORKS AT GRAYS, ESSEX.
Through the courtesy of Messrs. Hilton, Anderson, Brooks & Co., the writer had an opportunity to visit in detail their works at Grays, under the guidance of the resident director, Mr. Alfred Brooks. The present firm was formed by a union of the old firms of Hilton, Anderson & Co., and Brooks, Shoobridge & Co. They have four plants, two of them small; the other two, at Grays, on the Thames, and Halling, on the Medway, are quite large plants. The firm produces annually about 800,000 barrels of cement (Note 7), and has the largest American trade of any English house.
The works at Grays are directly on the Thames, some 22 miles below London, and are shown in plan in the figure (Note 8). Vessels of moderate draft can load directly at the wharves. The clay comes from the mouth of the Medway, some miles below, and is very expeditiously unloaded from the barges by means of a clam-shell dredging bucket which is carried by a 7-ton jib crane. The crane runs on a high level track on the wharf and drops its load into cars running at a lower level alongside the barge. It is by turns yellow or blue in color, but quite pure and free from foreign matter.
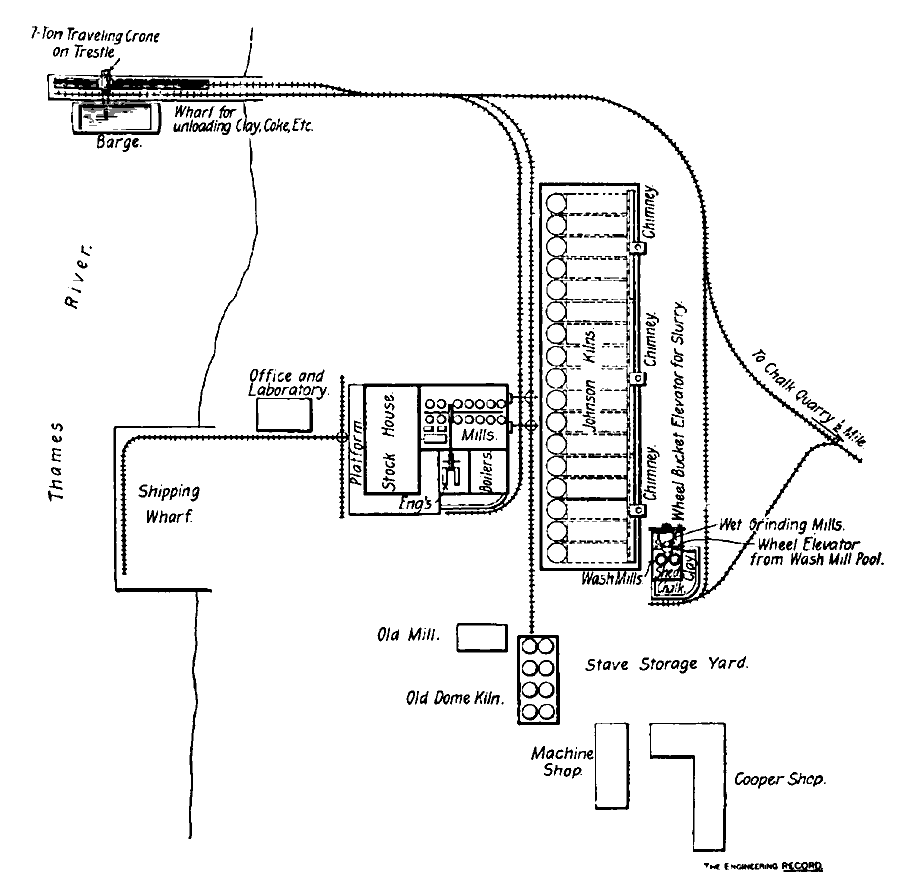
The chalk quarry is in the hillside some three-quarters of a mile back from the water front. Here there is a working face of 50 to 75 feet of white chalk, said to be 98 per cent. pure carbonate of lime. It is quite soft, readily breaking in the fingers and readily disintegrating in water in the wash mills. Its only drawback is the flints, which occur in regular beds, some five or six feet apart, and making clearly defined outcrops across the working face of the quarry.
The process of mixing the raw material is the semi-dry, or Goreham method (Note 9). In this process the clay and chalk are thrown into the wash mill and mixed in a rather thick slurry containing but 40 per cent. of water. On passing from the wash mill, the slurry is ground wet between buhrstones (sic) and then goes directly to the drying chambers of kilns of the Johnson type. The Johnson kiln, it will be remembered, is simply an intermittent kiln having a long drying chamber (or chambers) between the kiln and the chimney. The wet slurry is thus dried by the products of combustion of one charge, and the kiln is then recharged by simply taking up the dried slurry in the chamber and placing it in the kiln. It is evident that a process so simple and so direct could only be carried out with very pure and uniform raw materials. The fuel used is coke from the London gas works.
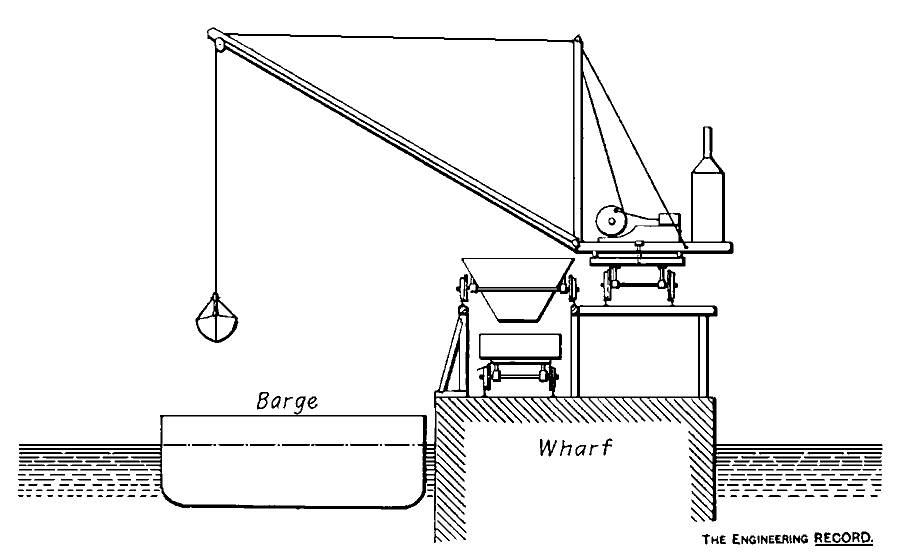
The balance of the works are much the same as at all other cement manufactories. The crushing and grinding machinery for the clinker, the stock-house and loading and shipping departments, differ only in details at different plants.
Two things of notable excellence about the plant are the power-house (Note 10) and the cooper shop. The engines are compound condensing engines of the Corliss type, with rope transmission directly from the flywheel. This rope transmission is apparently held in high esteem in Europe, the writer having found it in all the cement plants he has visited. Usually the ropes are hemp and 1¾ to 2 inches diameter. At Grays they are of special long fiber cotton. There are about ten or twelve strands leading from the flywheel to the pulley on the main shaft of the mill, and they appear to be in first-class condition after a service of eleven years. They transmit 300 horse-power.
The cooper shop has a full complement of tools for turning out barrels rapidly. One novel feature is the printing of the brand (Note 11) and label directly on the barrel heads. This is done in two over-lays on each head and is evidently much better than paper labels pasted on, which may or may not stay—often the latter.
THE FRANCIS WORKS AT CLIFFE.
The Francis cement is quite an old brand, having been well known in America for twenty years. It has a prominent place in a long series of experiments reported by Mr. W. W. Maclay, M. Am. Soc. C. E., in a paper read before the Society in 1878 (Note 12).
The writer had the pleasure of visiting the works in company with the resident director, Mr. Vitale de Michele, M. Inst. C. E. They are situated on the south side of the Thames, in Kent, some 30 miles from London. They are three plants (Note 13), one located directly in the chalk quarry, the other directly on the river front, mile away, and a third between these two points.
The chalk is all quarried in the first plant, while the unloading of the clay (from the Medway) and the shipping is done at the second. The raw materials are precisely the same as at Grays—white chalk, Medway clay and London gas coke. The kilns are of the same general type, and the only difference in process is that at Cliffe the raw materials are mixed with more water in the wash mills instead of by the Gorham (sic) process of thick slurry and wet grinding (Note 14). The power plant here is also excellent. The works in the chalk quarry present a most picturesque appearance, surrounded by the high white walls of chalk. Indeed, the blacksmith shops, stables and other minor offices are in excavations or caves directly in the chalk presenting a very unique appearance inside and out.
These two works, as described above, fairly represent the English cement industry as it exists to-day. Pure raw materials, simple direct processes, and the absence of the Continental bureau of "Controle" (Note 15), are its characteristics. The natural advantages possessed by English manufacturers on the Thames are evidently very great, the location and shipping facilities, all things considered, perhaps unsurpassed anywhere in the world. What these plants could do if remodelled on lines of the best modern practice is evidently now the question for English manufacturers to consider. American manufacturers would jump at such a chance without a moment's hesitation.